108" (2.74M) JAGENBERG VARIDUR SLITTER REWINDER REBUILT LIKE NEW
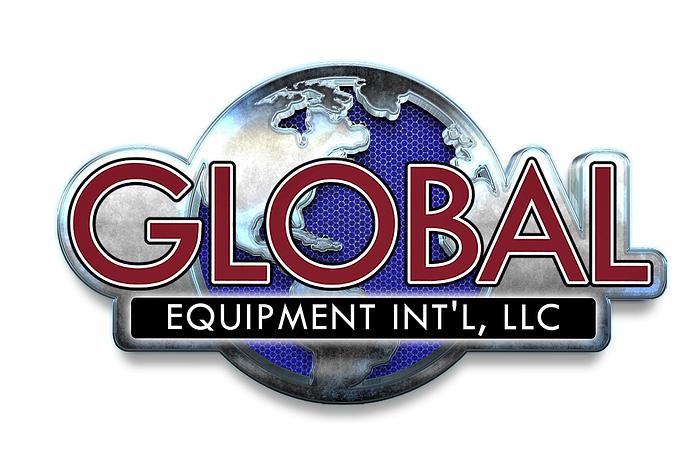
No longer available
108" (2.74M) JAGENBERG VARIDUR SLITTER REWINDER REBUILT LIKE NEW
Description
106271
One (1) used 108" Jagenberg Varidur Two Drum Slitter Rewinder. Complete Rebuild by Experienced New Manufacture :
Tension Range 2-6 PLI
Maximum Trim 104"
Roll Face 108"
Maximum Rewind Diameter 60"
Rewind Core Size 3"
Number Slitters Four(4)
Mill Voltage 460/3 Phase/60/ 50 HZ
Control Voltage 24V/1 Phase/60/50 HZ
Mill Air Supply 75 SCFM @ 25 PSIG
Slitter Section
The slitter section is a wrap shear cut type and is rear mounted.
The top slitters are pneumatically actuated from the console or individually from the slitter manifold. The slitters are mounted on a dovetail rack and are manually adjusted. Four (4) rear slitter bands which are clamped to the included rear mandrel pneumatically, and are manually adjusted. The rear mandrel is driven from a 7.5 hp AC motor. Four (4) Class III front slitter assemblies.
The before slitter roll is mounted on two (2) load cells for tension sensing.
Air lubricated trim guides are also provided for interfacing with existing trim removal system.
Spreader Rolls
One (1) spreader roll is positioned before slitting with penetration and bow direction adjustment. One (1) fixed bow spreader rolls is positioned after slitting mounted on the frame.
Winder Drums
Two (2) 18" diameter dynamically balanced steel drums.
Shaftless Chucking Assembly
Two new (2) shaftless chucking assemblies mounted on acme threaded spindles with 12" of deckle width adjustment per side. One (1) 3" diameter bore hydraulic cylinder per assembly is provided for chucking and unchucking. Deckle adjustment is by local handwheel with locking screw. Chuck assemblies are mounted to carriages, guided by cam followers with eccentric wear adjustment.
The two (2) 3" core chucks run on anti friction bearings.
All necessary hydraulic and electrical controls are included for "Chuck/Unchuck" functions and machine interlocks.
Shaftless Chuck Lift Assembly
Two (2) hydraulic lift cylinders each with mounting brackets and clevis, all necessary electrical and hydraulic controls are included for "Raise/Lower/Hold/Counterbalance" functions and machine interlocks.
Rider Roll Assembly
One (1) belt driven steel rider roll.
Two (2) rider roll carriage assemblies guided by cam followers with eccentric wear adjustment and two (2) spherical bearing housing assemblies.
Roll Ejector Assembly
One (1) activated dump roll designed to eject finished rolls onto lowering cradle. Roll ejector is interlocked so that it will not function until the roll chucks have been disengaged and rider roll raised.
Lowering Cradle/Nip Barrier Guard
The cradle assembly consists of full width plate to support the ejected roll and see through grating strategically placed for maximum visibility. It is raised and lowered by cylinders on each side.
In the lowered position, the cradle is near floor level and provides operator accessibility to the winder for threading, core loading, etc. The cradle has a slight pitch to roll the finished roll to the next handling operation.
In the vertically raised position, the cradle acts as a rugged nip barrier capable of restraining the rewound roll in the winder. As added safety, the cradle has two very heavy duty up latches to prevent accidental lowering of the cradle.
The entire operation is manually controlled with all necessary interlocks for safe operation.
Hydraulic Control
One (1) hydraulic pump 10 GPM @ 1000 PSI variable volume pressure compensated with maximum volume stop, 460/3/60/50 HZ, 20 HP, 1750 RPM, TEFC motor with coupling and adapter. One (1) hydraulic reservoir 60 gallons with liquid level, thermometer, suction strainer, and return line filter. One (1) manifold six (6) stations with six (6) direct control valves and gauges, 0 1500 PSI and dual flow controls, one (1) pressure reducing valve with reverse check, one (1) pressure reducing valve solenoid operation, one (1) relief valve set @1000 PSI, six (6) check valves.
Safety Features
Fail safe pneumatically disengaged latches for rider roll and lowering cradle prevent lowering if power is lost. Also, the pilot operated check valves are used in pneumatic and hydraulic circuits for further protection.
Photo electrics protect operators by stopping auto roll ejection cycle if operator is in a hazardous area, when cleared cycle resumes.
All guards are provided, and all wiring, piping, etc. are enclosed in the side frames and covered with panel doors.
Bench board Control Assembly
One (1) operator's console with all necessary controls to be incorporated into a HMI touch screen. Provisions for modem connection for drive/PLC system to facilitate remote troubleshooting is also provided.
Rider Roll Programmed Nip Control
One (1) Allen Bradley PLC Controlled system with set points for "Starting Load" (reads out in pounds), one (1) input for "Start to relieve diameter" (reads out in inches) and one (1) input for "Minimum Load Diameter" (reads out in inches). Also includes one (1) readout for indicating actual rider roll weight (as seen by rewinding roll) throughout set. One (1) position transmitter is included with mechanical interface to rider roll synchronizing shaft for roll diameter input. One (1) output transmitter with interface to lift cylinder.
Web Tension Control
One (1) PLC controlled system with PID control of web tension includes inputs or PLI (pounds/linear inch) and web trim width. Also includes one (1) readout for actual PLI or total pounds of tension throughout the set.
Drum Torque Programming
Allows operator to program the torque sharing between the two drum roll drives to give the best roll structure. Based on operator inputs, more torque is applied to the front drum at the start of the roll and then is slowly transferred to the rear drum. Includes function key/keypad inputs for front and rear drum load (in % of full load amps).
CRT Control
"Touch Screen" Terminal for mounting in bench board. The following will be programmed within the Touch Screen:
2 pages of twenty four (24) different recipes each for PLI, torque sharing and rider roll loading
1 page of torque sharing input
1 page of line speed parameters
1 page of rider roll input
1 page of fault/diagnostic information
1 page of operator assistance for machine operation (general)
Drives and Motors
Drum Drives
Two (2) 50 HP digital AC drive, two (2) 50 HP AC motors, one (1) isolation transformers.
Slitter Drive
One (1) 7.5 HP Digital AC drive, one (1) AC motor and motor starters are included.
All above drive components are mounted in NEMA 12 enclosure.
Unwind
Several options available depending on application. Price to be determined.
Specifications
Manufacturer | JAGENBERG |
Model | VARIDUR |
Condition | Used |
Stock Number | 106271 |
Width | 108.0 in |
Rewind diameter | 60.0 in |